Amber Lewey
Updated: Mar 20, 2024
An Introduction to Equipment Inventory Surveys
Equipment surveys are essential to building owners and AEC professionals to track assets, ensure accurate planning, and support efficient planning, design, and construction coordination.
First, What is an Equipment Survey?
An equipment survey is a systematic process undertaken to catalog, assess, and document all specified mechanical, electrical, and plumbing (MEP) or specialized systems within a building or project site.
The main deliverable of this process is an accurate and up-to-date equipment inventory list. This list will contain every relevant piece of equipment that an organization is interested in.
Dependent on the building type, other relevant equipment may include items such as:
Laboratory Equipment in hospitals, labs, universities, or industrial complexes.
Recreational equipment at schools, gymnasiums, or sports facilities.
Laundry equipment such as washers, dryers, and support infrastructure.
Environmental Control Systems such as air purifiers, dehumidifiers, or certain types of rainwater collection systems.
Key Aspects of Equipment Surveys
Equipment surveys are foundational to the lifecycle management of a building. They provide insights that influence decision-making in maintenance, renovations, as well as compliance.
Inventory Creation and Management
This involves compiling a comprehensive list of all equipment and systems within a facility, ensuring an organized approach to asset management.
Project Planning
Equipment inventory surveys are often conducted prior to a renovation, upgrade, or addition. This gives the AEC team the insights they need to execute on the project plan.
Asset Lifecycle Maintenance & Budgeting
Detailed condition assessments allow for accurate budgeting for maintenance, replacements, and upgrades.
Condition Assessment
Condition assessments focus on classifying (or validating) each item's operational effectiveness, efficiency, and physical state. The purpose is to provide the owner with a clear picture of equipment health.
Compliance Verification
Checks are carried out to ensure all machinery complies with the latest building codes, safety standards, and environmental regulations.
Risk Mitigation
Identifying equipment that is obsolete, damaged, or non-compliant can prevent potential hazards and operational failures.
Types of Equipment Surveys
Depending on your building type, an equipment survey may cover a range of components from HVAC systems, lighting, kitchen equipment, water heaters, and elevators, to safety and security equipment. Here are some of the most common domains you may be called to survey:
Mechanical Systems Surveys
Focus on heating, ventilation, and air conditioning (HVAC) systems, plumbing, and other mechanical equipment. The survey aims to assess the condition, capacity, and efficiency of these systems.
Electrical Systems Surveys

Evaluate a building's prime power sources, redundant power sources, electrical panels, wiring, lighting systems, and other electrical equipment. This is crucial for understanding the capacity of the electrical system and identifying any upgrades needed to meet new requirements.
Energy Audits
While not strictly a survey of physical equipment, an energy audit involves a thorough examination of a building's energy use, including the performance of HVAC systems, lighting, and other energy-consuming equipment. The goal is to identify opportunities for energy savings and efficiency improvements in equipment or building envelope.
Technology and Communications Systems Surveys
Examine existing technology infrastructure, including data cabling, telecommunications equipment, server rooms, and audiovisual systems. This survey type is essential for planning upgrades, integrating new technology systems into an existing building, or in assessing data security.
Safety and Security Equipment Surveys
Assess the condition and adequacy of fire safety systems (sprinklers, fire alarms), security systems (cameras, access control), and other safety-related equipment. This is vital for ensuring the building meets current safety standards and regulations.
Environmental Systems Surveys
Includes the assessment of systems that impact the building's environmental footprint, such as waste management systems, renewable energy installations (solar panels, wind turbines), and water conservation systems.
Laboratory Equipment Surveys
In hospitals, labs, universities, or industrial complexes, a laboratory equipment survey assesses the condition, functionality, and safety of scientific equipment. This can include everything from basic lab apparatus to sophisticated instruments like spectrometers, microscopes, centrifuges, and safety equipment (fume hoods, bio-safety cabinets). Such surveys ensure that the equipment meets current research needs and safety standards, facilitating accurate data collection and experiments.
Recreational Equipment Surveys
At schools, gymnasiums, or sports facilities, recreational equipment surveys focus on inspecting sports and fitness equipment, including gym machines, athletic field equipment, playground structures, and swimming pools. These surveys assess the safety, condition, and suitability of the equipment for its intended use, helping to prevent injuries and ensure compliance with safety standards.
Laundry Equipment Surveys
In facilities where large-scale laundry operations are a necessity, such as hospitals, hotels, or large residential complexes, surveys of laundry equipment are critical. These surveys examine washers, dryers, ironing machines, and support infrastructure for water supply and waste management. The goal is to ensure efficiency, safety, and the capability to meet the high demand for laundry services.
Biomedical Equipment Surveys
In healthcare facilities and research institutions, surveys of biomedical equipment are crucial. This includes devices for patient monitoring, diagnostic imaging (e.g., MRI, CT scanners, X-rays), surgical instruments, and therapeutic appliances. These surveys focus on ensuring the equipment meets the stringent regulatory standards for healthcare, is in good working condition, and is safe for both patients and healthcare providers.
Chemical Handling and Storage Equipment Surveys
In laboratories, manufacturing plants, and industries where chemicals are used or produced, surveys assess the safety and adequacy of chemical handling and storage equipment. This includes chemical fume hoods, storage cabinets for flammable or hazardous materials, gas cylinder storage facilities, and spill containment systems. The surveys aim to ensure compliance with environmental and safety regulations, preventing chemical accidents and exposures.
Cleanroom Equipment Surveys
In facilities requiring controlled environments, such as semiconductor manufacturing, biotech research, and pharmaceutical production, cleanroom equipment surveys evaluate the performance and condition of the cleanroom facilities and equipment. This includes air filtration systems, laminar flow hoods, cleanroom workstations, and contamination control systems. These surveys are essential for maintaining the strict cleanliness and contamination control standards required in these environments.
Data Center Equipment Surveys
For organizations with significant IT infrastructure, surveys of data center equipment assess the condition and performance of servers, storage systems, networking hardware, and backup power supplies (e.g., UPS systems). These surveys also evaluate the effectiveness of cooling systems and environmental controls to ensure optimal performance and reliability of critical IT assets.
Material Handling Equipment Survey
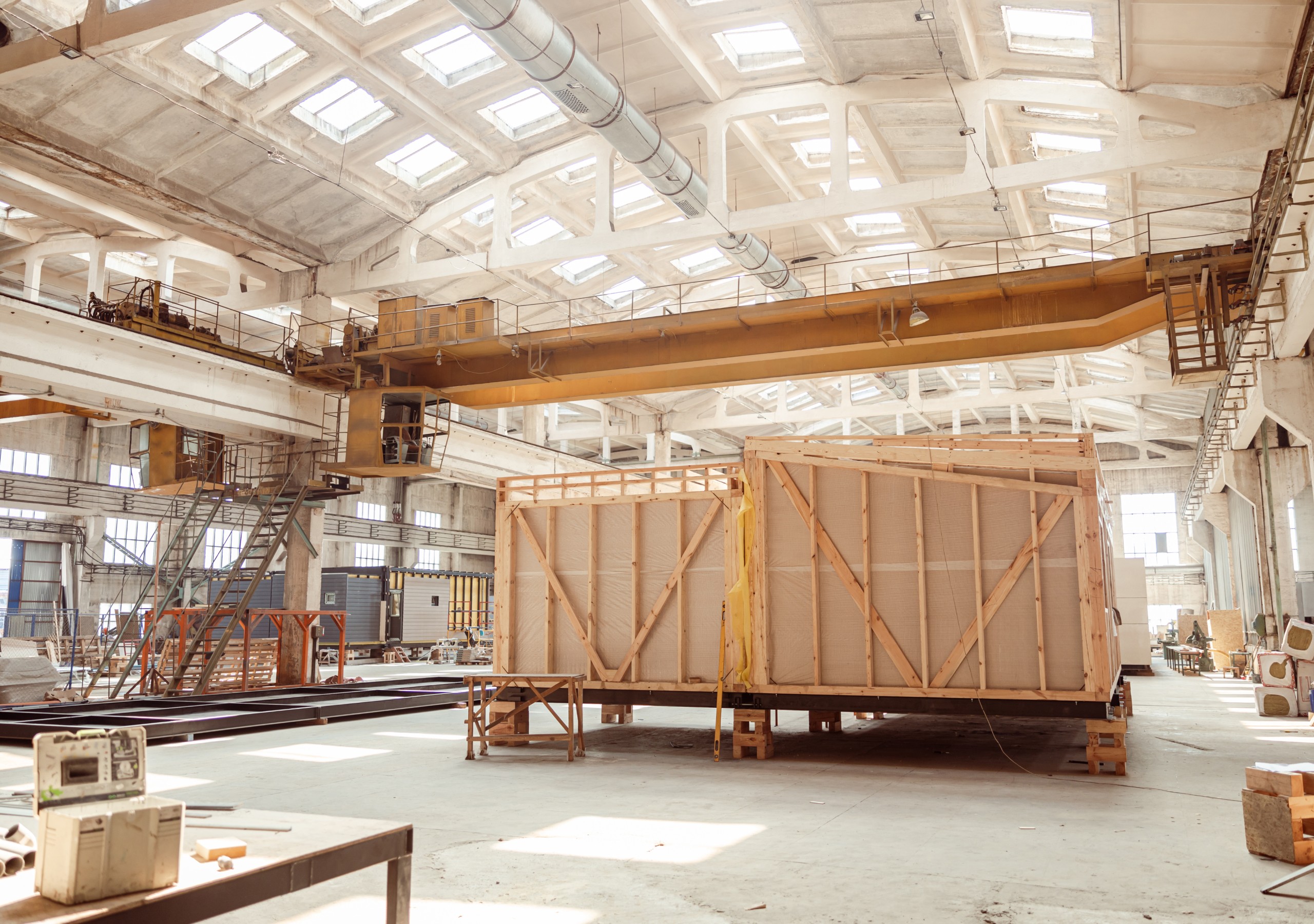
In warehouses, distribution centers, and manufacturing facilities, surveys of material handling equipment focus on the safety, efficiency, and condition of forklifts, conveyor systems, pallet jacks, and automated storage and retrieval systems (AS/RS). These surveys help in optimizing the logistics and operational efficiency of material handling processes.
The Equipment Survey Process Explained
So, you've been assigned to conduct an equipment survey. A structured approach ensures that all assessments are thorough, accurate, and most important: you are collecting the right data points.
This process can be broadly categorized into four key steps: preparation and planning, walking the site, report creation, and follow-up (as needed). Here is what you should expect:
Step 1: Preparation and Planning
Your first step involves defining the scope of your survey. This entails specifying which systems and equipment will be assessed and by when. Identifying any stakeholders, coordinators, and/or potentially impacted parties.
To facilitate this, gather any existing documentation and schematics detailing the building's equipment layout. Sometimes this documentation may be limited to outdated models or floorplans or even just a spreadsheet of equipment.
These documents are crucial for understanding as much about the current configuration to plan the assessment, even context can be critical. Organizing your survey around the building will provide a solid foundation to build on.
Pro-Tip: Organize your data collection around the building’s model or floorplan. This will make it easier for the architects and engineers to visualize where everything is and help the GC in creating the best work sequence for the project.
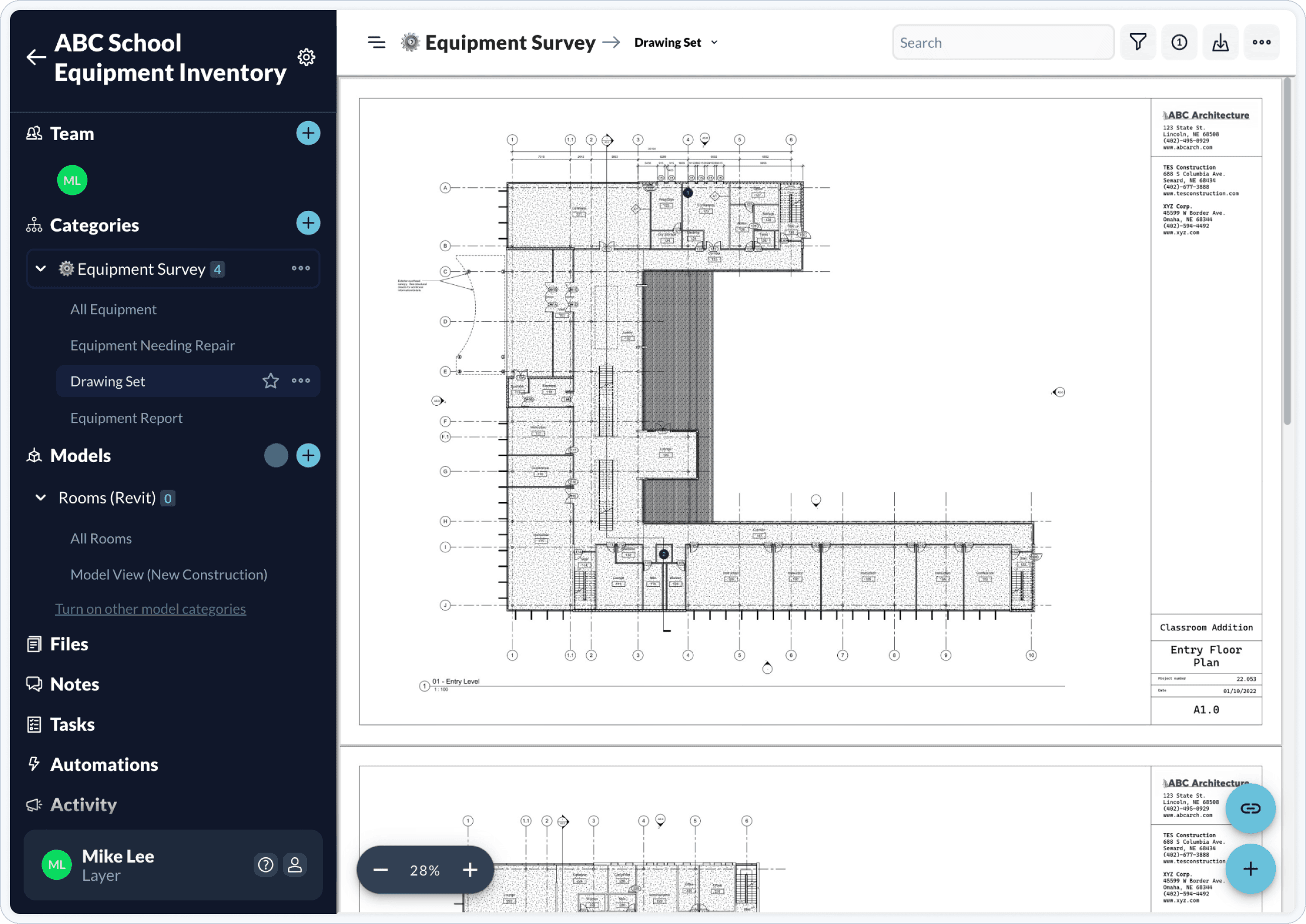
View Layer Equipment Survey Template →
Following the preparation of documentation, a multidisciplinary team is assembled. You should include professionals with expertise in the relevant systems, building codes, and project requirements.
This team is responsible for planning and executing the site visit, where the actual assessment takes place. A diverse skill set within the team ensures a comprehensive evaluation of the building's systems, taking into consideration technical performance, compliance with building codes, and alignment with the project's objectives.
Step 2: Walking the site
While the multidisciplinary team will be focused on collecting information prior, during, and after the equipment survey it is important to remember the site or building stakeholders.
During planning you have created a list of teams or individuals that are required to be coordinated with, are preferred to be included in these plans, or may be impacted during the effort. Communicate with each party what the intention is, the time and finish of your activities, and specify requests.
Depending on the intended outcome of the survey, walking the site should be approached similar to creating a schedule for your week. There are some locations that will have to be assumed as by appointment and there are some locations or areas that are easiest to capture all the details at once.
While walking the site, approach observations, preferably with pictures, as burst photography. In other words, take more photos and notes than you know you need. Equipment surveys are core to maintaining the life of the asset and oftentimes the devil is in the details…or an obscure portion of a photo that caught signs of water penetration.
Step 3: Work Planning
Work planning adapts to the project's specific goals. For renovation or expansion projects, survey data is crucial. It guides the general contractor in work sequencing. This ensures tasks are logically ordered for efficiency.
Assessing equipment condition is another key survey objective. Data collected prioritizes necessary interventions. This is vital for effective resource allocation. Urgent needs are addressed promptly, with less critical issues planned accordingly.
For building maintenance surveys, findings inform a maintenance schedule. This identifies aging or inefficient equipment. A timeline for necessary interventions is outlined. This approach enhances system longevity and performance, supporting overall maintenance strategy.
Step 4: Follow-Up and Continuous Improvement
Data from the survey guides project planning, maintenance scheduling, and continuous improvement efforts, with an emphasis on prioritizing work based on the project’s parameters.
As the professional conducting the survey, you may be asked for further information or clarification from your survey. This will typically happen in the form of an RFI. Luckily you conducted your survey via an organized process. Responding to an RFI will be as simple as pulling your notes and responding as requested!
Conclusion
An equipment survey is a critical element in the management and optimization of building systems within architecture, construction, and engineering.
By adopting a meticulous approach to equipment surveys, professionals in these fields can ensure the longevity, efficiency, and compliance of the built environment, safeguarding the well-being of its occupants and the sustainability of its operations.