Rodrigo Urrutia
Updated: Jan 12, 2024
An Intro to Project Controls in the AEC Industry
In construction, the unexpected is common, but never welcome. The root cause is often poor communication. Project Controls processes are put in place to facilitate better communication between GCs, Owners, Architects and other stakeholders.
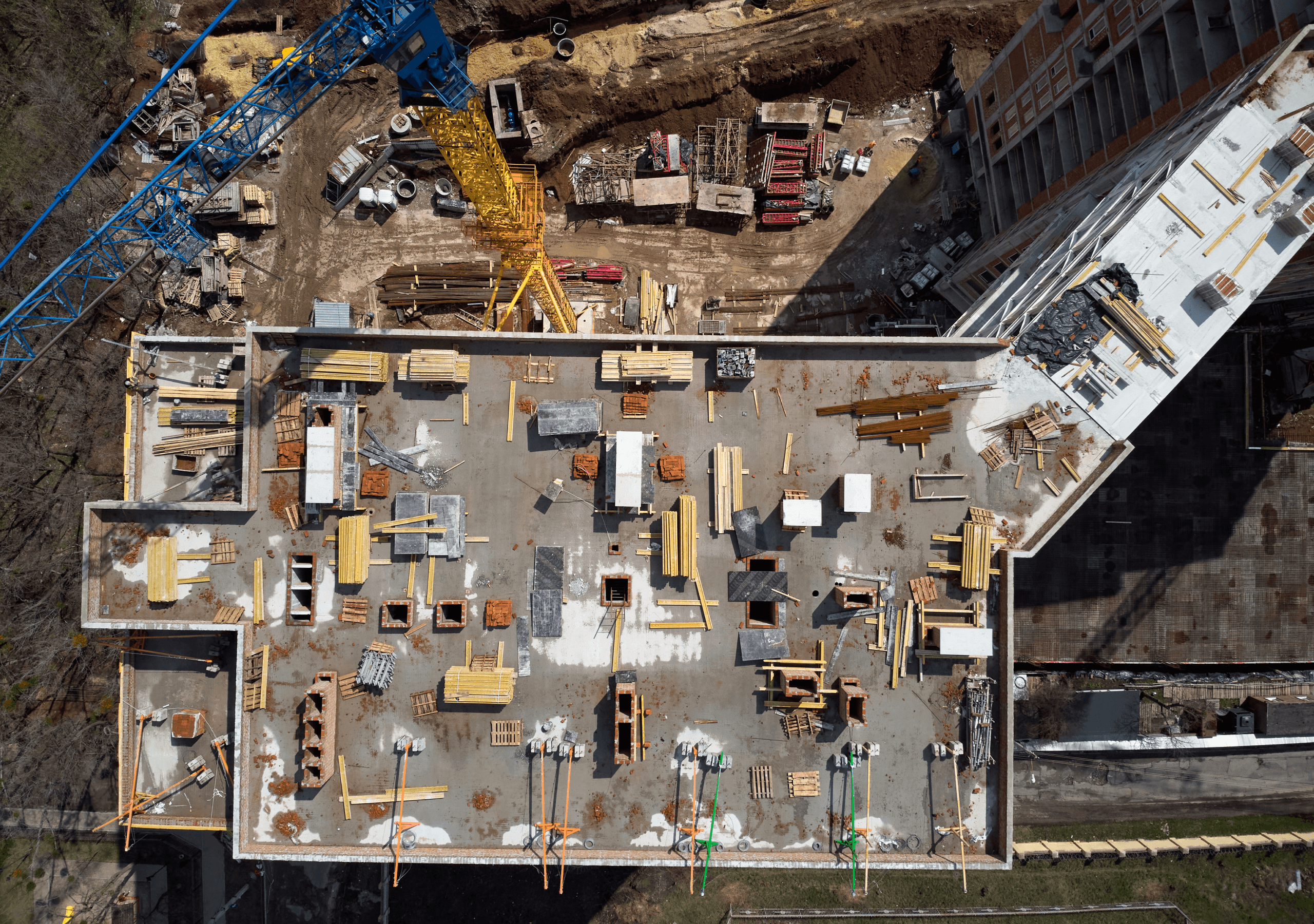
First, what is Project Controls in Construction?
Project controls is a collection of tools, processes, and systems that contractors utilize to manage the allocation of time and financial resources in a project. Each component of project controls concentrates on a specific element of the project plan. Examples include schedule, resources, and potential risks.
The purpose of the Project Controls Team is to prevent the unexpected from occurring. This encompasses anything that could cause the project to go over schedule or budget.
What responsibilities does Project Controls have in a construction project?
Both a General Contractor and the Project Owner will have a Project Controls Department. This team handles a smorgasbord of activities. This can include planning, monitoring, and control across various project variables including project, time, quality, risk, and potentially others.
Project Controls is unique in each organization. However, there is a general litmus test you can use to determine if project controls will be involved in a particular step, phase, or activity:
| Does [insert activity here] interact with the project schedule or budget? If so, project controls will be included.
The Project Controls Process
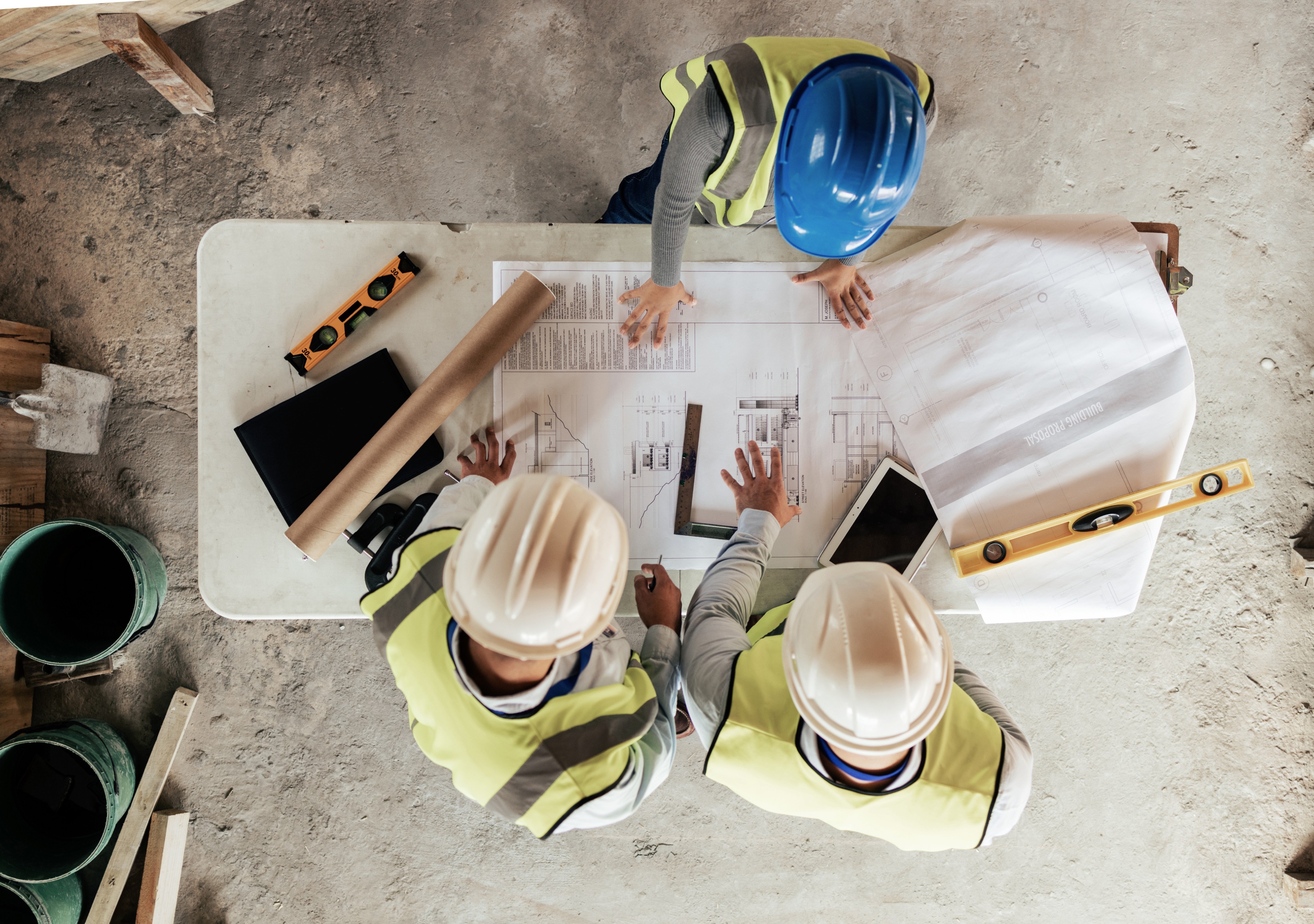
The project controls process encompasses several pivotal steps:
Planning and Scheduling:
As an architect or engineer you’ll likely first encounter project controls during planning. The owner and GC will have representatives that align with the technical staff to create a detailed project plan. Based on the contract structure and delivery model this will lead to timelines, and resource allocation.
A project plan should outline at minimum:
The project's technical scope
Contractual requirements
Deliverables
Resource allocation
Work breakdown structure (WBS)
Timelines
Project Budget
Risk assessment
These plans serve as your project's north star. They set the direction, allocate resources, and should provide a clear understanding of what specifically needs to be accomplished.
Timelines and Milestones
Within planning, Project Milestones are the contractor and project owner's primary focus. Milestones represent significant points in a project's progression. These may include groundbreaking ceremonies, foundation completions, structural framing, and more.
Financial considerations are the main reason milestones are considered so important. Clients typically pay contractors based on milestones outlined in the project contract and project plan. Late delivery can lead to penalties or forfeited payments.
TLDR: Milestones are very important, because that is when stakeholders like the General Contract are due payment.
Resource Allocation
Once timelines and milestones have been determined it’s time to allocate resources in order to meet these deadlines. Resource allocation is a very delicate balance. This involves determining where and when labor, materials, and equipment, are needed. Efficient resource allocation is a key to completing a project successfully.
Today, availability of on-site labor may be a primary concern, particularly in large projects. As an architect or engineer you can offer guidance to your client on the best way to overcome these challenges. Sometimes it may make sense to build portions of your project off-site then carefully sequence the assembly instead of using traditional stick built techniques.
Project controls professionals will collaborate with project managers to ensure that the right resources are available when required. This might involve coordinating with suppliers to ensure timely material deliveries or scheduling skilled labor for critical phases.
No construction project unfolds entirely without issues
Contingency planning is the theoretical safety net that a project controls professional will employ during planning. This involves identifying potential risks and developing strategies to mitigate them.
For instance, if a project involves constructing a high-rise building in an earthquake-prone region, contingency plans may include how materials are stored on site in case of a natural disaster. Identifying these risks and planning for them in advance minimizes disruptions to your project during construction.
Cost Management
In order to stick to the budget, the project controls team will employ a variety of cost management practices. This starts with obtaining accurate cost estimates up front, but also budget monitoring, and robust cost control strategies to thwart budget overruns are just as important.
At the core of cost management lies art the science of cost estimation which is also a bit of an artform. Construction projects are complex and multifaceted endeavors, and accurate cost estimates are the compass that guides financial decision-making.
Project controls professionals collaborate closely with estimators who assess every component of the project, from materials and labor to equipment and overhead costs. These estimates provide a foundation upon which budgets are constructed. The accuracy of these estimates is paramount, as any miscalculation can ripple through the project's financial landscape.
Once your project is underway, the budget becomes a living, breathing entity.
It requires constant vigilance and monitoring. Project controls professionals employ sophisticated tools and systems to track expenditures against the budget.
Budget monitoring in the project involves:
Regular financial reports: These provide a snapshot of where the project stands financially.
Variance analysis: It identifies disparities between planned and actual expenditures.
Cost forecasting: Predicting future costs based on current trends and potential changes.
These activities allow project controls professionals to detect early warning signs of budget overruns and take corrective actions promptly.
Cost Control Strategies
Effective cost management isn't just about keeping tabs on expenses; it's also about implementing robust cost control strategies to ensure that the project stays within budgetary boundaries.
Project cost control strategies may include:
Change order management: Properly assessing the impact of design changes on costs.
Value engineering: Identifying cost-effective alternatives without compromising quality.
Procurement optimization: Negotiate favorable terms with suppliers and subcontractors while understanding the true materials cost. Include transportation, storage, and logistics to gain a competitive advantage.
Resource allocation: Ensuring that resources and project team members are used efficiently to avoid waste.
Pro Tip - We recommend integrating your work plan with your cost control strategies. Specialty labor can be incredibly expensive. The equation to keeping your project life cycle and budget under control? Have materials ready to as soon as your specialized trades or installers get to the site.
Risk Mitigation
Cost management isn't solely about dealing with known expenses; it's also about preparing for the unexpected. Construction projects are susceptible to various risks, from weather-related delays to supply chain disruptions.
Project controls professionals collaborate with risk analysts to identify potential financial pitfalls and develop strategies to mitigate them. This may involve creating contingency budgets or purchasing insurance to cover unforeseen events.
In essence, cost management in construction project controls is a delicate balancing act. It requires the precision of a financial expert, the vigilance of a detective, and the foresight of a strategist.
Risk Assessments
Given the inherent uncertainties in construction, risk assessment and mitigation strategies are indispensable. A risk assessment is not merely a component of project controls; it sets project boundaries.
Identifying Risks
The first step in risk assessment is identifying potential risks. This involves a comprehensive examination of every facet of the project, from design and procurement to execution and delivery. Project controls professionals work in tandem with risk experts to catalog an extensive spectrum of potential threats.
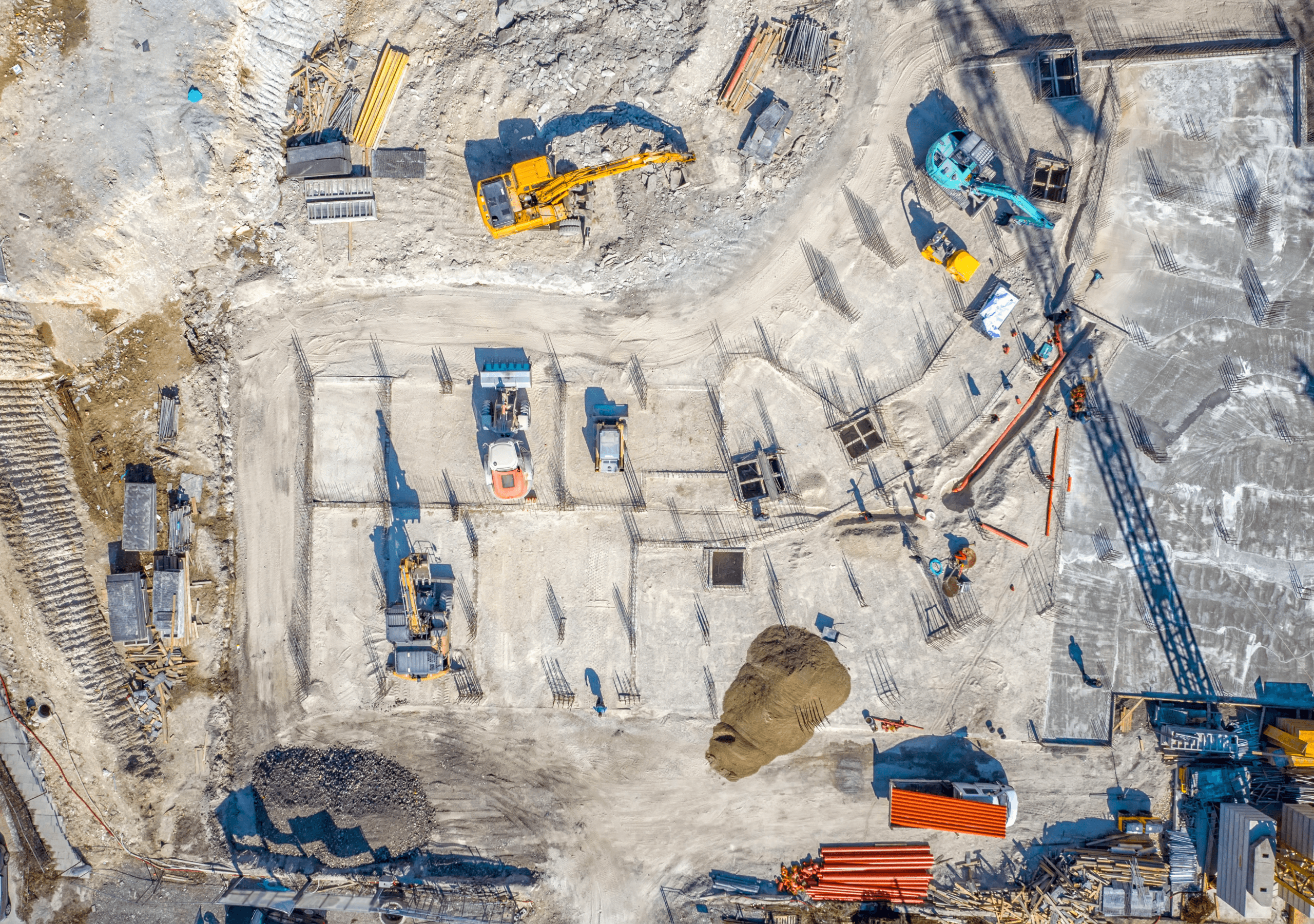
Common risks in construction may include:
Weather Delays: Unforeseen meteorological events can disrupt construction timelines.
Supply Chain Disruptions: It's difficult to predict supply chain issues in real time. Disruptions in the supply of materials or equipment can lead to delays and cost overruns.
Labor Shortages: A scarcity of skilled labor can impede project progress. Project Controls and Project Management need to accurately forecast and plan for labor in areas with few construction workers.
Regulatory Hurdles: Evolving regulations may create compliance issues or pose legal and financial risk.
Design Changes: Modifications in project design can trigger budgetary and scheduling challenges.
Risk Quantification: How you can measure the unmeasurable
Once risks are identified, the next challenge is quantifying them. This involves assessing the likelihood of each risk occurring and estimating its potential impact on the project. These quantitative measures create a risk profile that allows project stakeholders to prioritize their attention and resources.
Risk quantification may involve:
Probability Analysis: Assigning numerical probabilities to each risk scenario.
Impact Assessment: Determining the potential financial and temporal consequences of a risk event.
Sensitivity Analysis: Evaluating how variations in one risk factor may ripple through the project's overall risk landscape.
These quantitative insights enable project controls professionals to focus their efforts on the most significant risks, developing strategies to address them proactively.
Mitigation Strategies: How your team can navigate the storm you may not know is approaching
Risk assessment is not a passive endeavor; it's about developing robust strategies to mitigate identified risks. Project controls professionals collaborate with risk management experts to craft tailored mitigation plans for each risk category.
There's many ways that you can mitigate risk to a project. The most common that we employ include:
Contingency Planning: We establish a reserve budget or timeline during the project to address specific risks if they materialize.
Insurance Coverage: If you can't afford to take the hit, you should insurance can help protect the bottom line. We typically employ insurance policies to safeguard against financial losses due to unforeseen events.
Contractual Protections: During negotiation you can push for contract terms that allocate risk appropriately among all the project stakeholders.
Alternative Sourcing: It's a good idea to identify alternative suppliers or resources to mitigate supply chain risks. Things happen, having a backup is key.
Continuous Monitoring
Risk assessment is not a one-time task but a continuous process that evolves with the project. Project controls professionals will monitor risk profiles throughout your project's lifecycle then adapt mitigation strategies as circumstances change.
This typically involves:
Regular Risk Reviews: Periodically revisiting and updating risk assessments.
Scenario Planning: Simulating potential risk scenarios to assess their impact on the project.
Response Planning: Developing response plans for emerging risks that were not initially identified.
Quality Control
Work sequencing and unforeseen risks are not the only challenge you may face. Quality control begins with defining clear and stringent quality standards that align with project objectives and industry best practices.
Key aspects of setting quality standards include:
Regulatory Compliance: Ensuring that the project adheres to all relevant codes, standards, and regulations.
Performance Criteria: Defining performance metrics for materials, equipment, and workmanship.
Client Expectations: Aligning project quality with client expectations and contractual obligations.
Continuous Improvement: Establishing processes for ongoing quality enhancement.
Quality Assurance: Your team should seek to build a culture of excellence
Quality control is not a one-time audit. Instead, it's a pervasive culture embedded within the overall project team. This requires proactive quality assurance measures to prevent defects rather than merely detecting and rectifying them.
Quality assurance entails:
Process Standardization: Implementing standardized procedures to ensure consistency in project execution.
Training and Skill Development: Equipping project personnel with the requisite skills and knowledge to deliver quality work.
Materials Testing: Rigorous testing and inspection of construction materials to confirm compliance with specifications.
Work Inspections: Regular inspections of work processes to identify and rectify quality deviations promptly.
Quality Inspections
To enforce quality standards, a robust inspection regime is imperative. Quality control professionals conduct meticulous inspections at various stages of the project, from material procurement to final delivery.
Key components of quality inspections include:
Material Inspections: Verifying the quality and integrity of materials upon receipt and throughout their use.
In-Progress Inspections: Monitoring work in progress to identify and rectify deviations from quality standards.
Final Inspections: Comprehensive evaluations before project handover to ensure adherence to quality benchmarks.
Documentation Control: Maintaining detailed records of all inspections, deviations, and corrective actions.
Non-Conformance Management: Correcting Deviations
Despite the best efforts, quality deviations may occur. Effective quality control includes a robust system for identifying, documenting, and addressing non-conformance issues promptly.
Non-conformance management involves:
Issue Identification: Promptly identifying and documenting quality deviations, including their root causes.
Root Cause Analysis: Investigating the underlying reasons for non-conformance to prevent recurrence.
Corrective and Preventive Actions: Implementing corrective actions to address immediate issues and preventive measures to forestall future non-conformance.
Continuous Improvement: Using non-conformance data to enhance quality control processes continually.
Pro-Tip: You can use software tools like Layer to track RFIs and corrective action followup.

Preview the Layer App RFI Template →
The Litmus Test: Your Client's Acceptance
Ultimately, the client plays a pivotal role in quality control. Their acceptance of the project's quality is the ultimate litmus test of success.
Client acceptance entails:
Quality Validation: Client representatives conducting their inspections to confirm that the project meets quality expectations.
Documentation Handover: Providing the client with comprehensive documentation, including quality records, for their reference.
Defect Resolution: Addressing any quality concerns or defects raised by the client promptly and professionally.
Project Closure: Formalizing the project closure once the client is satisfied with the delivered quality.
In essence, quality control in construction project controls protects the project's reputation and the can help assure client satisfaction.
Conclusion: Who to Navigate Construction Challenges
The construction industry is unique in that it produces highly bespoke products, but this leads to a fair share of challenges. One persistent issue is a major lack of transparency. Stakeholders often hoard information, given the enourmous financial stakes involved.
Opacity can lead to inaccuracies and inefficiencies in project management. Accurate and timely information is paramount for informed decision making. This directly impacts project outcomes.
A well thought out Project Control strategy is your best line of defence to overcoming inevitable project challenges. By embracing these methodologies and integrating technology, the construction industry can build faster and at lower cost. As a new project controls professional, you hold those keys to unlocking project excellence.