Mike Lee
Updated: Mar 11, 2024
Everything to know about Construction Punch Lists
Learn how to manage construction punch lists to track final tasks, ensure quality standards, and complete projects efficiently.
First, what is a punch list in construction?
In construction, a punch list is a list of work that needs to be fixed before the project is finished. This is the final QA/QC gate before a building is ready for occupancy. Punch lists are typically generated during a final inspection of a project.
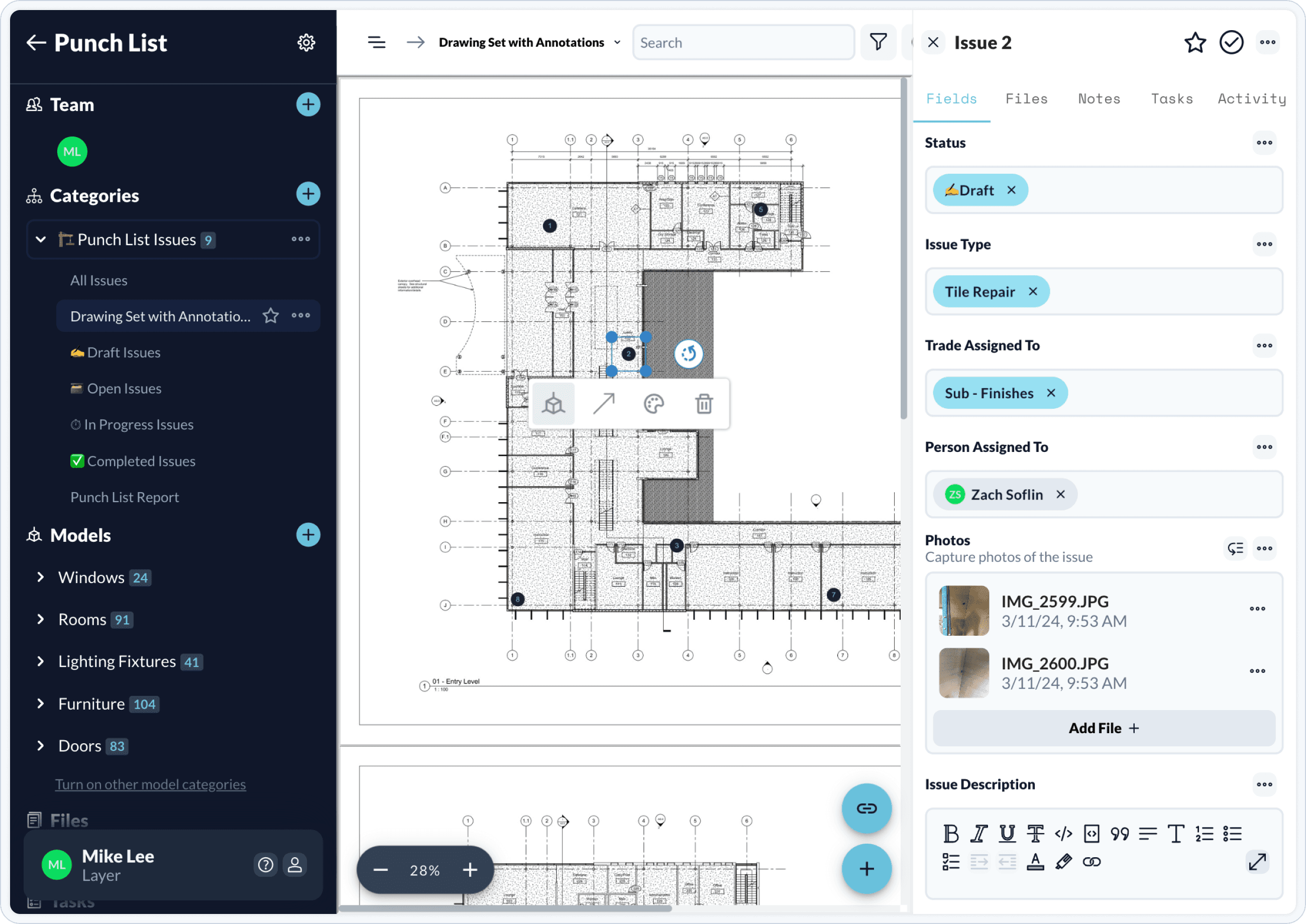
Understanding the Punch List
The term "punch list" originates from the practice of punching a hole in a physical checklist next to completed items at the end of a project. The architect and builder would use identical lists stacked on top of each other to create duplicate records.
In some regions, a punch list may also be known as a snag list. Although the terminology differs, the concept remains consistent: a compilation of tasks requiring resolution before project completion. Most importantly, a contractor must complete or correct these items before they receive final payment.
The Project Closeout Process is a Team Effort
In addition to the general contractor and owner, architects, engineers, and other stakeholders may be involved in the project closeout process. For instance, in a commercial property application, a tenant may also be an interested party in signing off on the work.
During the inspection, the stakeholder team identifies any defects, incomplete work, or unresolved issues. This information is used to create a list of corrective actions.
What Are Punch List Items?
Punch list items are typically minor tasks identified as non-conforming with the contract specifications. These items can be functional or qualitative in nature, ranging from minor aesthetic concerns to significant structural issues. This document, listing "work that does not conform," acts as a final checklist for the builder or contractor.
What does a punch list typically contain?
A punch list typically contains items to that need to be fixed, added, or tested. Punch list items will vary depending on your type of project. A punch list for a new factory will be different from one for a small residential construction project. Common items to test will fall in the following categories:
Doors
Windows
HVAC
Mechanical
Plumbing
Appliances
Installed Equipment
Examples of items to fix will likewise vary. Here are some common examples
A light switch does not work.
A wall socket is not hooked up.
Tile or glass is cracking.
Here are some examples of items that may need to be added:
A sink needs caulking applied.
Paint needs to be touched up in an area.
A fixture does not match the others or is missing a cover.
However, you don't need to conduct an inspection to be proactive!
Rolling Punch Lists
A rolling punch list addresses issues as they arise in a project rather than at the end. This approach allows for the immediate resolution of problems, reducing the size of the final punch list and enabling a faster project closeout and handover.
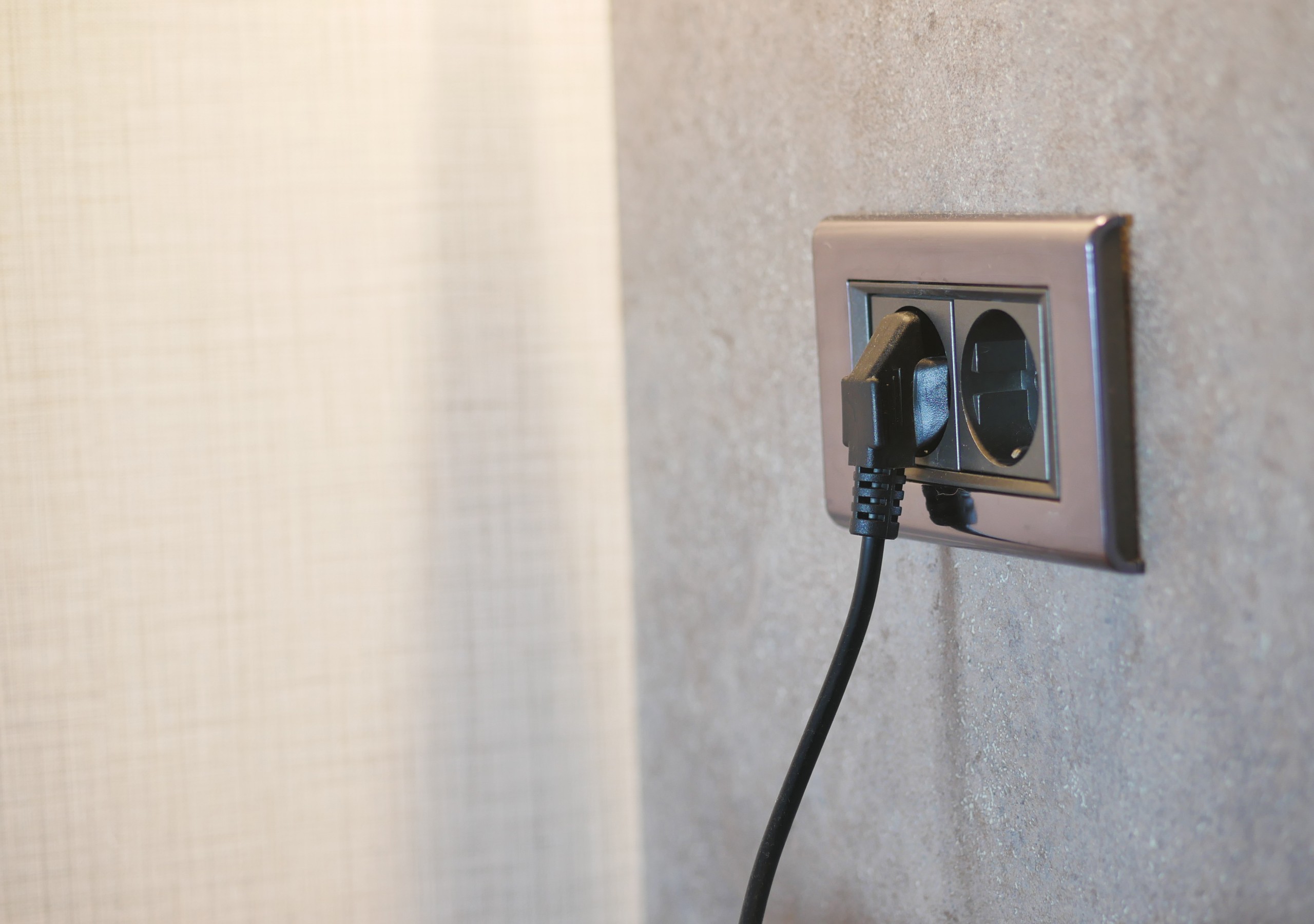
We suggest choosing a punch list tool that is available on mobile, desktop, and tablet devices. This ensures that workers in the field can easily collaborate with other project team members in the office.
Punch List Tools and Templates
Punch list templates are an effective way to ensure all punch list items are recorded then resolved the same way. Using a template ensures a standardized format, and makes it more likely that all relevant details are captured according to your firm's internal best practices.
Software tools can help keep everyone on the same page.
Watch this quick video to see how Layer can help you punch out punch list items faster: Learn More
What should contractors and builders know about the punch list process?
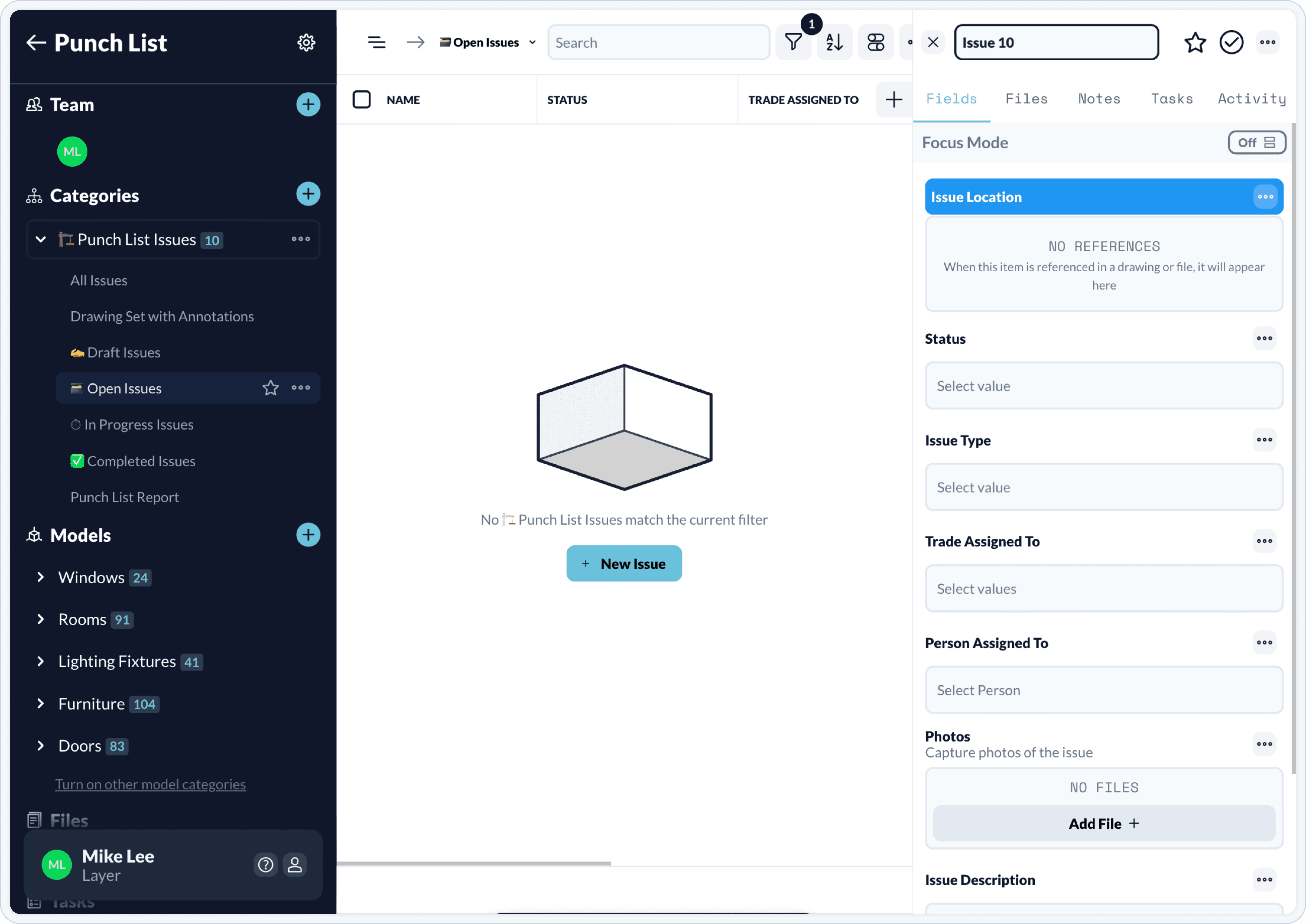
The Importance of Punch List Items
Punch list items are crucial not only for ensuring a building's readiness for occupancy but also as a contractual step preceding final payment. Often, an owner will withhold retainage payments pending the completion of punch list tasks.
What is the responsibility of the General Contractor with punch list items?
Well, ultimately they're responsible for addressing all of them before they get paid. Even if the work has been subcontracted, the GC is in charge of coordinating any necessary remedies.
Creating internal standards and deploying them as a template ensures consistent quality project delivery. Layer lets you save your projects as a template to make this process a breeze.
Preview Layer Template: Preview Layer Template
Learn more about how Layer can streamline your punch list process with customizable templates.
When does the Punch List Process typically start?
When contractors judge the project to have reached the substantial completion phase, they may initiate a "pre-final" inspection. Ideally, the necessary punch list work will be minimal, paving the way for swift final completion and subsequent payment.
What Should Architects and Engineers do to ensure the Punch List Process goes smoothly?
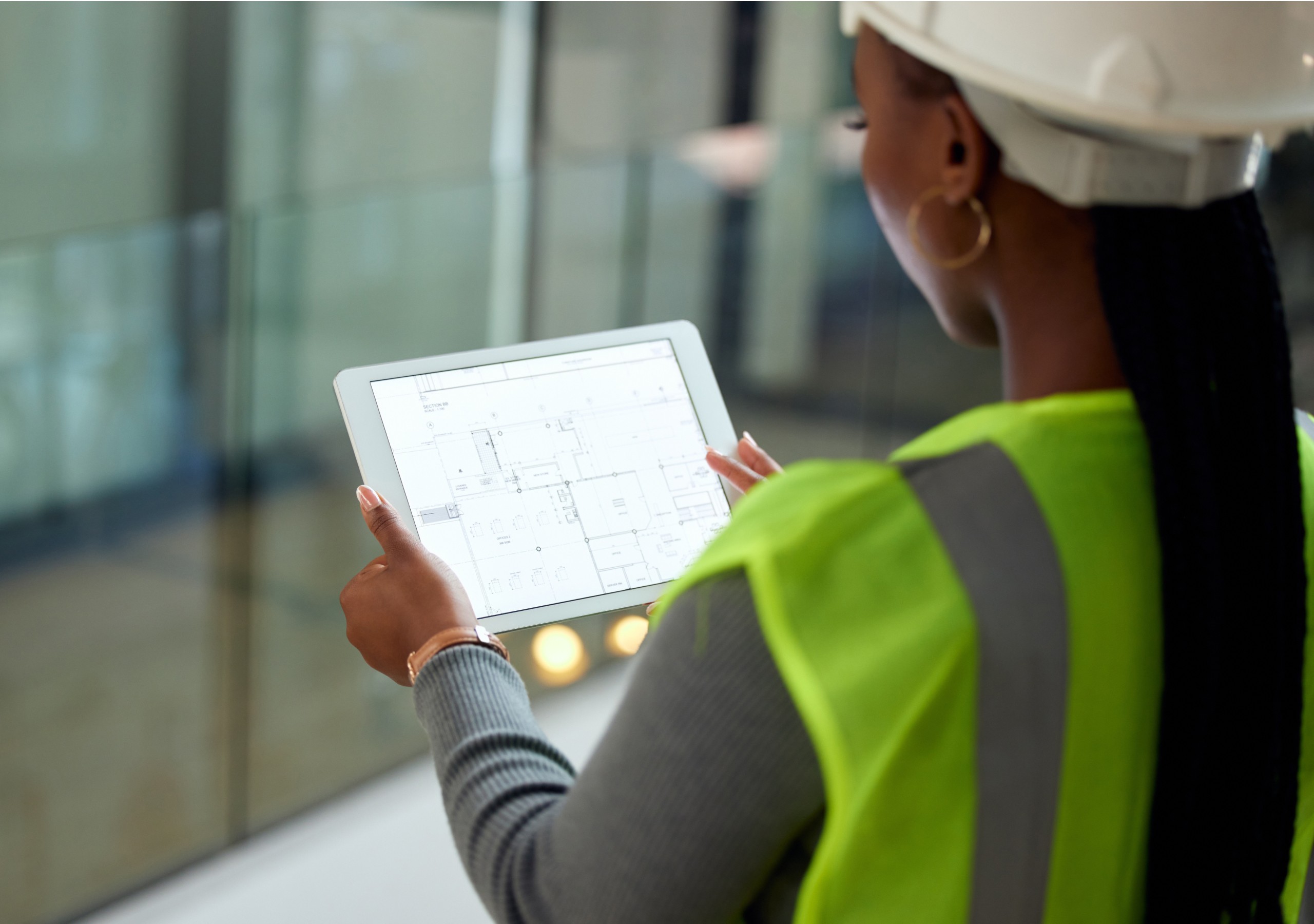
Architects and engineers should be aware of their role in the punch list process, including:
Understanding the Scope: They should understand the scope of the punch list items to ensure they align with the project specifications.
Coordination: They need to coordinate with the GC and other stakeholders to verify that punch list items are correctly addressed.
Documentation: Proper documentation is essential to confirm that all punch list items are completed satisfactorily.
You are typically acting as an agent for the owner during this process. It's important to put yourself in the owner's position. Is the building ready for occupancy? Your reputation ultimately rests on the quality work of a third party.
Conclusion: Each project has its own set of challenges. Using a collaborative punch list tool with built in templates can help everyone involved understand the final steps required to complete the project faster.