Ryan Shoop, RA
Updated: Dec 20, 2022
The Ultimate Guide to How to Specify Door Hardware | Expert Tips by Ryan Shoop
Join door hardware expert, Ryan Shoop, RA, as he walks us through how to specify door hardware. Read more >
How to Specify Door Hardware: A Comprehensive Guide for Architects
In this article, door hardware expert Ryan Shoop, walks us through the door hardware specification process.
As an architect, I find that it is often difficult to explain to non-architects what it is that an architect does. If you are an architect or engineer, I'm sure that you can relate!
It is even more difficult to explain what I do as a door hardware consultant, but let's try:
How about "I choose what hinges to put on the door"?
Not perfect, but it's a step in the right direction.
Before we review how to specify door hardware, let's define what door specifications are.
1. What are Door Hardware Specifications?
A door hardware specification is a written list of all door hardware products for installation on each door in a construction project. The spec also includes criteria for the selection, testing, and installation of those products. Examples of door hardware include hinges, closers, locksets, stops, gasketing, and many other products.
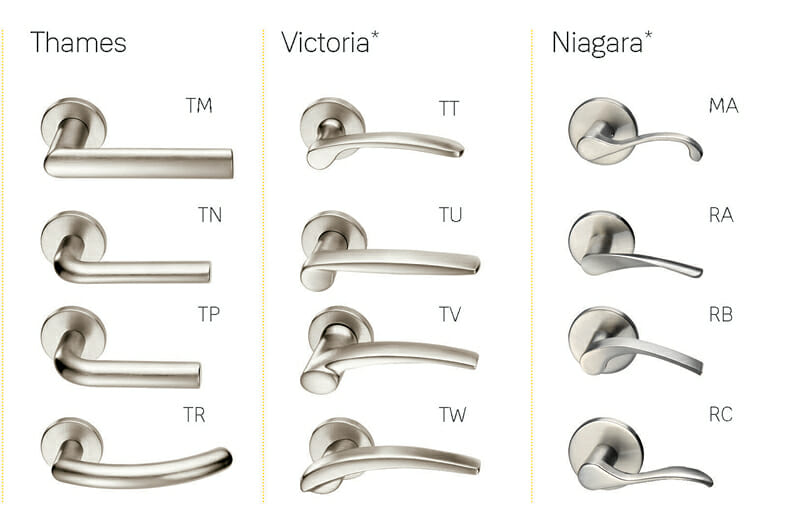
Image Credit: Yale / ASSA ABLOY
2. Who typically does this work?
The door hardware specification is a necessary element of the contract documents for a construction project.
Architects can write them, but they are very often written by specialized door hardware consultants. These consultants provide the specification to the architect for inclusion in their project manual (spec book). Or on their drawing sheets (sheet specs).
Many door hardware consultants who serve the pre-construction sector are employees of door hardware manufacturing companies. They typically write their door hardware specifications based around their employer's products.
Many others are employees of door hardware distributors who may represent more than one manufacturer. Or door and hardware subcontractors who service the pre-construction (design) phase and the construction phase.
There are also independent door hardware consultants.
3. At what point in the project schedule do you specify door hardware?
This is up to the architect or whoever is the primary decision-maker responsible for the schedule of the project documentation.
In my opinion as an architect and door hardware consultant, the ideal time to generate the door hardware specification is after the building plans are settled enough that there will be no further changes to the doors. This is usually sometime in the second half of the Design Development (DD) phase of the project.

Image Credit: Monograph
It would not be appropriate to begin the specification earlier than that. Because even minor adjustments to a door can have a major effect on what hardware is appropriate for that door.
However it is possible—and sometimes very beneficial—to take a preliminary look at some general door hardware criteria early in the project to establish a basic design intent.
Big picture questions of scope are helpful to ask early in the DD phase.
Questions such as: Will there be any electronic access control (EAC) hardware? Or which does the client/designer prefer, aluminum entrance doors or all-glass doors?
It is possible to begin writing the door hardware specification later than the ideal time. However. it is important to not wait too long. Because just like every construction spec, it takes time to write the door hardware spec.
The door hardware spec may need to be issued as an addendum to the contract documents if this isn't taken into account early on. This could result in change orders from the contractor (this is not what the project's client wants to hear).
4. What is the process for specifying door hardware?
(And other things to consider, best practices, tips, etc.)
The Goal of the Door Specification Process
The goal of the specification process is to deliver a design for doors with hardware that meet the client's goals of function, appearance, cost, and durability.
The hardware on a door determines how the door functions, and how it looks. Also, the hardware selection has important implications for the construction cost (first cost) and durability (lifetime costs).

Image Credit: AJ Brown Imaging
4.1: Study the Project and Gather Information
At the beginning of the process, the specifier needs to study the project documents (in particular, the plans and door schedule) to understand the basic setup.
It is also helpful in the beginning to collect input from the design team about any specific design requirements they have for the door hardware.
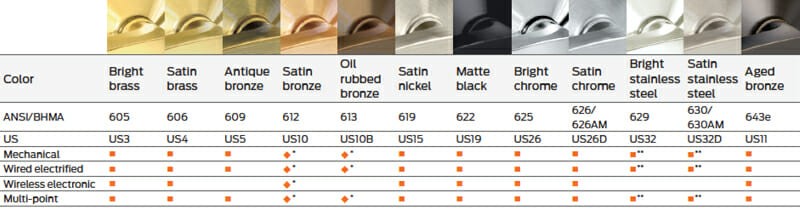
Image Credit: Schlage
For example: This could include things such as electronic access features, finishes, lever styles, preferences to avoid specific types of hardware, and many others.
4.2: Preliminary Analysis and Rough Sorting
The specifier then begins sorting the doors into broad categories by identifying critical parameters applicable to the doors.
The categories will later be further sorted into the individual hardware sets assigned to each door.
Some of the important parameters to consider are exterior/interior, door/frame material, fire-rated/non-rated, and single/pair. Which parameters are critical will vary from one project type to another.
For example: if all doors in a project are not fire rated, then fire rating is not a helpful parameter to consider.
Sorting the doors into parameter-based categories is helpful.
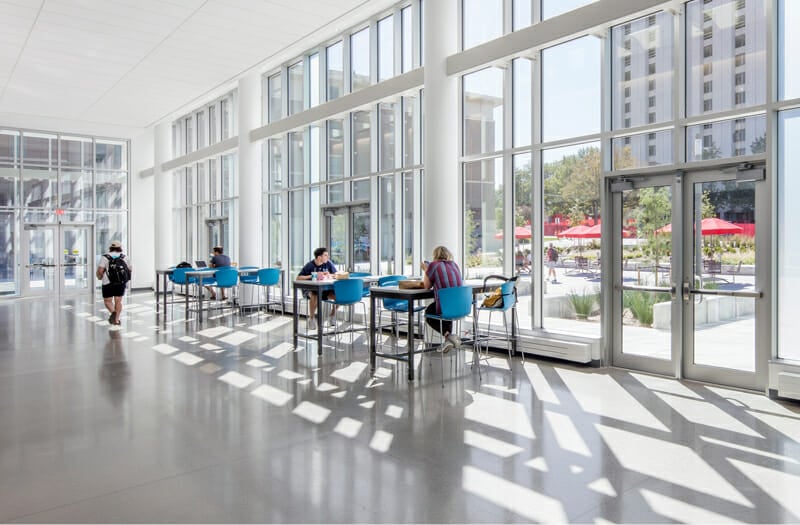
Image Credit: AJ Brown Imaging
For example the hardware used on an exterior door should be different than hardware used on an otherwise similar interior door. Likewise, the hardware used on an aluminum entrance door is different than hardware used on a hollow metal door in hollow metal frame.
4.3: Feedback from Project Team
The specifier begins to review and understand the doors on the project. They develop a list of questions about design intent. This is for the architect, client, or other team members such as the interior designer or security consultant.
Door hardware is an extreme niche specialty. It is likely that up to that point in the project, nobody else on the project team will have thought to ask the questions that the specifier comes up with.
For example: Let's take a simple question such as will this door always be left unlocked during the building's operating hours and locked at other times? The door hardware specifier needs to know the answer to this question in order to select hardware that will function appropriately.
However, finding the answer may require input from multiple parties. Such as the architect, the client representative, the client's operations team, the client's commercial tenant, etc. and so on.
Effective and robust communication with the project team is critical to yielding a door hardware spec that meets the expectations of the stakeholders.
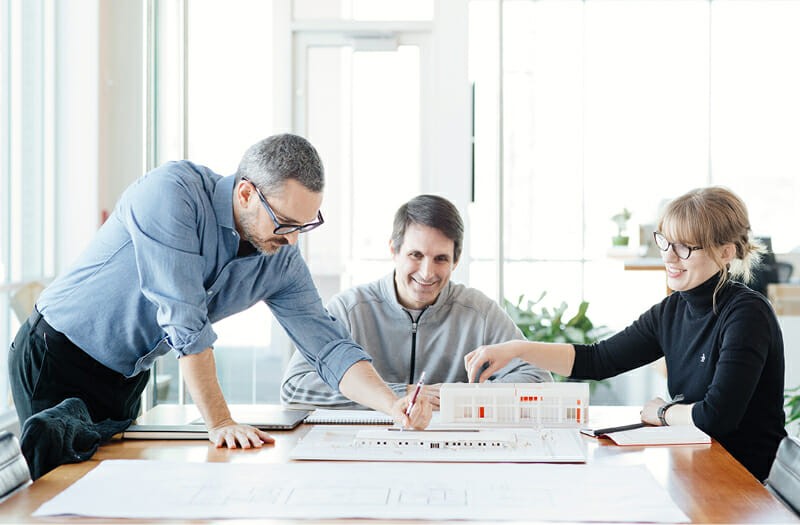
Image Credit: Dana Damewood
4.4: Drilling Deeper, Listing the Hardware Sets
From this point, the specifier further studies the individual doors. They also identify criteria that necessitate further dividing/sorting within the broad categories noted earlier into smaller more specific categories.
For example: there may be several doors that are hollow metal, interior, fire rated, passage function. Most of them are OK to use wall stops. But some of them need to use a different type of stop (such as overhead). This is because they don’t open against a nearby wall.
This act of sorting eventually produces the individual hardware sets.
4.5: Selecting Hardware Items
Once the specifier is reasonably confident that most of the hardware sets have been fleshed out, the specifier selects specific hardware items (either performance-based or proprietary) and generates the list of hardware items that belong in each set. The hardware sets are then assigned to each door in the door schedule.
The specifier should take care to keep the number of unique hardware sets to the minimum necessary. This simplifies the documentation, which greatly helps to avoid confusion during construction.
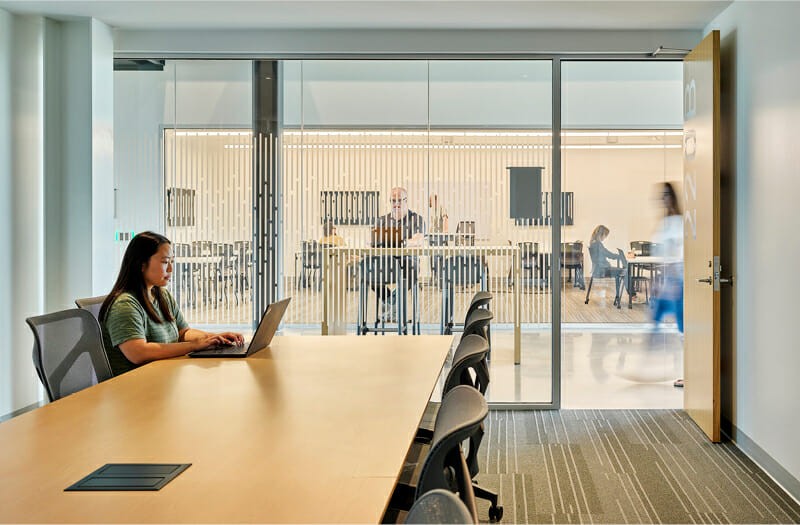
Image Credit: Michael Robinson
5. How does the door specifying process relate to the door schedule?
What form does the documentation take?
How does it relate to the rest of the project documentation?
Door hardware specifications appear in the contract documents as a book spec or as a sheet spec (specs on sheets).
In either case, the architect uses a "hardware set" column in the door schedule to indicate which hardware set to use on each door.
Sometimes the architect may wish to supplement the hardware description with additional text in the "notes" or "comments" column of the door schedule. Be careful with this tactic. It may result in conflicting information between the note and the hardware spec.
To Book Spec or Sheet Spec?
It is up to the architect to decide whether to specify the door hardware as a book spec or sheet spec. Often times, book specs tend to include more and better information in the Part 1 (General) and Part 3 (Execution) portion of the spec, as compared to sheet specs. In either case, the product information (Part 2) is usually the same.
Other than the "hardware set" column in the door schedule, ordinarily there is nothing else in the drawing set that describes the door hardware besides the hardware spec itself.
Sometimes for projects with highly customized doors and/or doors where aesthetics are a high priority, the architect or interior designer may wish to include elevation drawings of the doors that also depict some of the hardware.
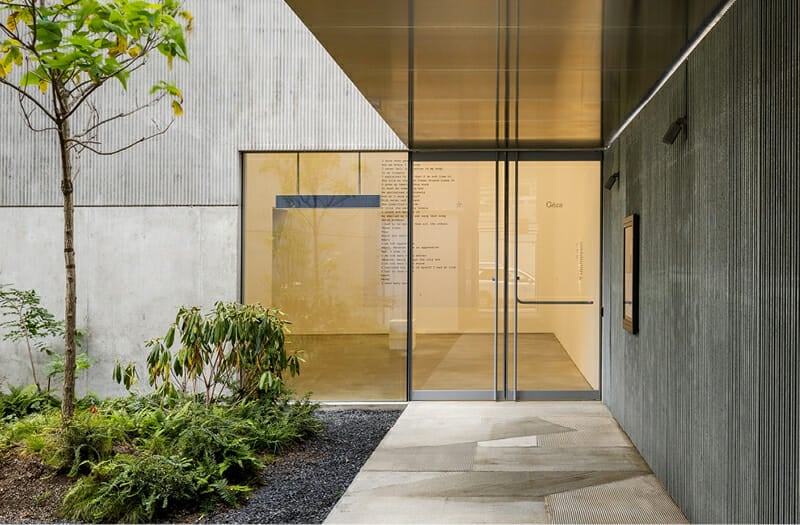
Image Credit: CR Laurence
Examples may be all-glass doors with "designer" pulls, or stile and rail doors with push/pull plates that the designer wants to align in a particular way.
Again, whenever there is duplicate information in the contract documents it is important to avoid disagreement between the drawings and the hardware spec.
6. What tools can the specifier use in this process?
The specifier needs some way to look at the drawings. But besides this, the specifier can get by with tools as simple as a basic word processing app, manufacturers' product data sheets, and catalogs.
A word processor is the “floor”. Specifiers can certainly produce acceptable deliverables for their clients using nothing more than that.
However, if this “floor” is the whole platform the specifier chooses to use, this forces them to rely heavily on their own internal knowledge along with a mountain of disorderly product documentation gathered from numerous manufacturers.
If the specifier chooses to build up from that very simple floor, there are solutions for simplifying, templating, and automating some aspects of the specification process.
Keeping a database of product data can be a helpful, time-saving strategy for the specifier.
A Relational Database Solution
It is one thing to generally know that a product exists and then go looking for it. It is very different to have a ready-made comparison of similar products from different manufacturers at your fingertips.
Product information tactfully linked directly into the specifications is a great time saver and a quality assurance tool. A relational database such as the Layer App is an essential tool to build this specifier’s platform.
Below are some screenshots of a simple door hardware spec that I copied into the Layer App from a previous project of mine. To set up this basic door hardware spec, I created two “categories” (Door Hardware Items and Door Hardware Sets), and one “view” (Door Hardware Spec).
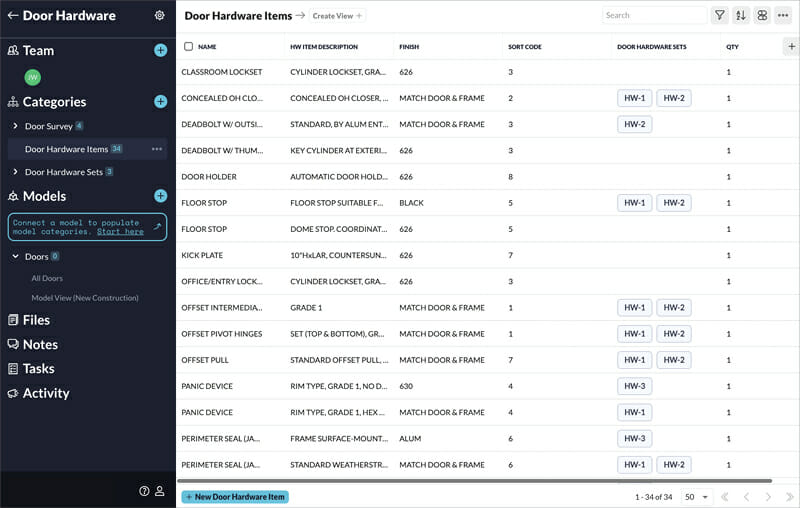
The Door Hardware Items category (above) is a list of every door hardware item in the project. These items link into the next category, Door Hardware Sets.

The Door Hardware Sets category (above) lists each hardware set. This includes the label (HW-1, HW-2, etc.), a brief description of the set, and the list of hardware items that are used in that set, which are linked in from the Door Hardware Items category. The label can be inserted into the project’s door schedule. I put this under a “hardware set” column to indicate which hardware set is used by each door.

The Door Hardware Spec view (above) draws the information from the two categories mentioned earlier and presents it in a format that can be copied directly into the finalized project specification and used as the door hardware schedule. (Note Layer has an in-app custom report builder which automatically fills in data).
Changes to individual hardware items automatically propagate wherever that item occurs. This is an excellent means of ensuring consistency of information, as well as a huge time saver to the specifier.
Conclusion
Door hardware specification is a challenging many-faceted task. It Is less so with well-tuned systems and the right tools. I hope this article shines a light in a corner of the design process that many in the AEC industry tend to shy away from.
About Ryan Shoop, RA
Ryan is an independent architectural door hardware consultant and architect, licensed in the state of New Jersey. Ryan represents over ten years of industry expertise and has overseen dozens of projects, from design to construction to completion.